فرآیند آبکاری الکتریکی اساساً برای رسوب دادن نیکل، طلا یا نقره روی جواهر آلات، چاقو و قطعات دوچرخه به کار رفت. مهارت علمی سازندان انگلیسی، آلمانی و آمریکایی و مرغوبیت ممتاز محصول آنها این فرآیند را عمومیت داد. امروزه آبکاری الکتریکی تا حدی توسعه یافته است که نه تنها مرحله نهایی تولید بعضی محصولات است بلکه برای ایجاد پوششهای محافظی مثل کادمیم، کروم یا اکسید آلومینیوم روی قطعات به کار می رود.
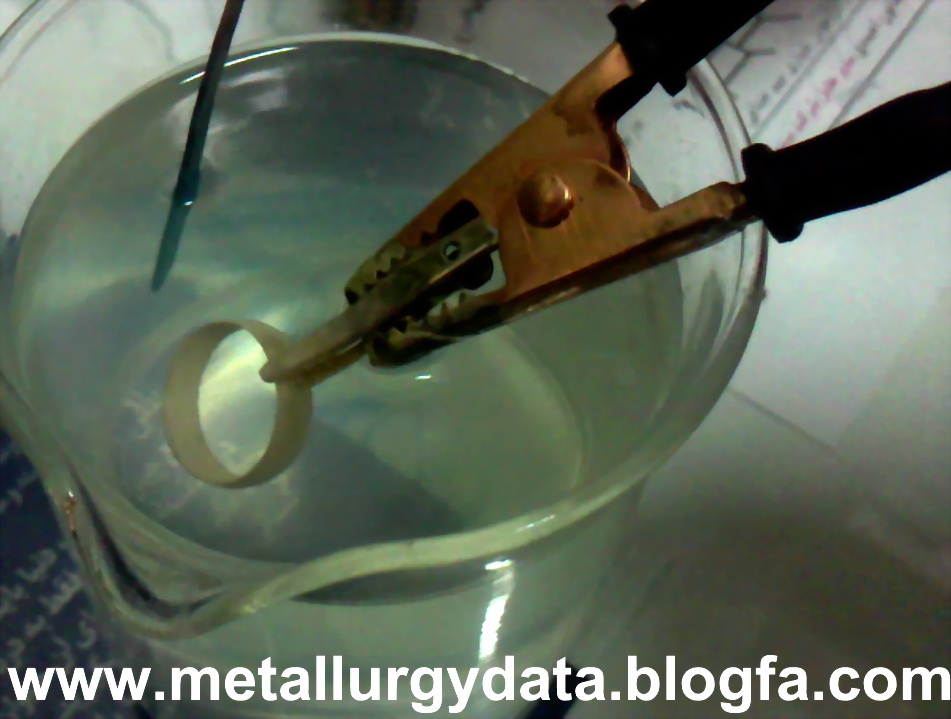
فرآیند آبکاری الکتریکی اساساً برای رسوب دادن نیکل، طلا یا نقره روی جواهر آلات، چاقو و قطعات دوچرخه به کار رفت. مهارت علمی سازندان انگلیسی، آلمانی و آمریکایی و مرغوبیت ممتاز محصول آنها این فرآیند را عمومیت داد. امروزه آبکاری الکتریکی تا حدی توسعه یافته است که نه تنها مرحله نهایی تولید بعضی محصولات است بلکه برای ایجاد پوششهای محافظی مثل کادمیم، کروم یا اکسید آلومینیوم روی قطعات به کار می رود.
اساس آبکاری الکتریکی به این صورت است که در اثر عبور جریان مستقیم از یک الکترولیت فلز محلول در آن روی کاتد رسوب کرده و متعاقباً مقداری از فلز آند وارد محلول می شود به این ترتیب الکترولیت ثابت می ماند. آبکاری الکتریکی برای ایجاد پوشش های تزئینی و محافظ، اصلاح سطوح ساییده شده یا اضافه ماشینکاری شده، قطعه سازی یا به عبارتی شکل دهی الکتریکی قطعات شکل پیچیده که دارای زوایای مقعر، ابعاد دقیق و سطوح طرح دار (مثل صفحات چاپی)هستند، عملیات آندکاری، تمیزکاری الکترولیتی، پرداخت الکترولیتی، اسید شویی آندی، استخراج و تصفیه فلزات به کار می رود.
ضخامت پوششهای رسوب ـ الکتریکی به دانسیته جریان، راندمان جریان و مدت زمان عملیات بستگی دارد. خواص فیزیکی تابع دانسیته جریان، دما، ترکیب حمام، کیفیت سطحی قطعه و عوامل افزودنی به حمام است. از این نظر نمکهای آبکاری الکتریکی اهمیت زیادی پیدا کرده اند به طوری که روز به روز تقاضای آنها افزایش می یابد.
کیفیت رسوب الکتریکی بر حسب کاربرد آن تغییر می کند اگر هدف از آبکاری این باشد که برای مدت کوتاهی از زنگ زدن فولاد جلوگیری شود ممکن است پوشش نازکی هم کافی باشد ولی اگر شفافیت رسوب نیز مهم باشد در این صورت کیفیت بالاتری طلب خواهد شد. کیفیت رسوبهای نازک از طریق آزمایش اندازه گیری ضخامت و مقاومت خوردگی تعیین می گردد.
کیفیت آبکاری به واکنشهای که در طول عملیات روی کاتد انجام می گیرند بستگی دارد. اگر حمام به طور صحیح آماده و تنظیم شده باشد واکنشهای فوق نیز مطلوب خواهند بود. ولی کلاً شرایط مناسب عملیاتی از نظر کاتد و حمام تولید رسوبی رضایت بخشی را تضمین نمی کند.
آماده کردن حمام:
اولین قدم برای آماده کردن حمام جدید این است که وان خالی کاملاً تمیز شود. ذرات و گرد و غبار از طریق جارو کردن و خشکانده خارج گشته و مواد روغنی توسط کهنه آغشته به حلال مناسب پاک شوند. وانهای پلاستیکی یا لاستیکی به تمیز کاری بیشتری نیاز دارند. وانهای چدنی ممکن است به رنگ کاری یا آسترکشی نیاز داشته باشند. وان عملیات بعد از اسیدشویی با آب آبکشی می شود. اگر وان بلافاصله مورد استفاده قرار نگیرد آن را با محلول 1% هیدرواکسید سدیم یا تری فسفات سدیم پر می کنند تا زنگ نزند. در غیر این صورت مقداری آب به آن ریخته و بعد ترکیبات دیگر اضافه می گردد. برای نمکهای حل شونده معمولاً 3/1 وان را پر می کنند ولی برای نمکهای سخت ـ حل شونده نظیر نمکهایی که به حمامهای غلیظ نیکل اضافه می گردند باید از 3/2 وان استفاده کرد. ترتیب اضافه کردن ترکیبات مهم است. برای مثال در آماده کردن حمام سیانیدی مس، سیانید قلیایی قبل از سیانید مس نامحلول به حمام اضافه می شود. ولی ترتیب اضافه کردن کربنات، نمک راشل یا سوزآور خیلی مهم نیست. نمکها و کلاً ترکیبات دیگر باید به طور آرام به حمام اضافه شده و همزمان محلول هم زده شود. این کار ممکن است به طوردستی و با یک بیلچه انجام بگیرد. در صورتی که نمکها سریع اضافه شوند ممکن است در اثر گلوله ـ گلوله شدن انحلال خیلی سخت انجام بگیرد.
بعد از انحلال کامل همه نمکها وزن مخصوص الکترولیت را توسط هیدرومتر بومه اندازه می گیرند. در صورتی که وزن مخصوص حمام مناسب باشد آبکاری آزمایشی روی چند نمونه انجام می گیرد. بدین ترتیب مشخص می شود که آیا می توان از حمام استفاده کرد یا ترکیب آن باید مجدداً تنظیم شود. برای مثال ممکن است pH و عوامل افزودنی به اصلاح نیاز داشته باشند یا تصفیه اولیه لازم باشد. بعد از اینکه ترکیب حمام در دامنه مورد نظر تنظیم گشته و آبکاری آزمایشی انجام گرفت آزمایش را برای شارژ کامل اجرا می کنند تا رفتار جریان از نظر ولتاژ، اشکالهای الکتریکی و تماس قلابها و آویزها به شمشهای اتصال چک شود. در آبکاری الکتریکی شستشو دادن، آبکشی، اسیدشویی و چربی گیری اهمیت زیادی دارد در اینجا هر کدام از عملیات فوق به طور مختصر توضیح داده می شود:
1)شستشو: این کار توسط انواع تمیز کننده های قلیایی انجام می گیرد انتخاب نوع آن به موادی که باید شسته شوند و همین طور روش شستشو (غوطه وری خالص یا با استفاده از سیستم الکتریکی)بستگی دارد. پاک کننده ها موادی چون فسفات سدیم، هیدرواکسید سدیم، سیلیکات سدیم، کربنات سدیم، بورات سدیم یا ترکیبی از مواد فوق هستند ولی موماً حاوی فسفات یا سیلیکات همراه با مقداری کربنات یا هیدرواکسید هستند.
در تمیز کاری الکتریکی قطعات ممکن است قطب آند یا کاتد باشند. تمیز کننده های آندی ترجیح داده می شوند چون ناخالصیهای فلزی نمی توانند روی قطعات رسوب کنند.
2)چربی گیری: قبل از شستشوی الکتریکی چربی گیری انجام می گیرد. به این صورت قطعات را در حلالهای سرد غوطه ور کرده یا در معرض بخار داغ قرار می دهند. بخار حلال روی فلز کندانس شده و چربی را حل می کند.
3)اسید شویی: در فرآیند های آبکاری برای تأمین سطح فعال باید فیلمهای غیرآلی سطح شامل پوسته های اکسیدی یا محصولات زنگ از سطح حذف شوند. در غیر این صورت چسبندگی رسوب به سطح کار ضعیف شده و ممکن است رسوب حفره ـ حفره و یا پوسته ـ پوسته گردد.
4)آبکشی: آبکشی ممکن است به صورت غوطه وری در آب جاری یا با استفاده از اسپری انام بگیرد. بعضی وقتها برای اطمینان از خارج شدن نمکهای سطحی ممکن است آبکشی تکرار شود.
جزئیات تمیزکاری قطعات فلزی:
سطح قطعات فلزی معمولاً حاوی گرد و خاک، گریس، پوسته های اکسیدی و مایعات خاص مصرف شده در فرآیند تولید است. چنانکه قبلاً گفته شد برای تأمین چسبندگی مطمئن بایستی هرگونه آلاینده ای که از تماس مستقیم محلول حمام با سطح فلزی جلوگیری می کند پاک گردد. علاوه بر این قبل از آبکاری باید شیارها و خراشها و یا پوششهای سطحی اصلاح شوند.
محلولهای تمیزکاری: برای پاک کردن مواد روغنی با گریس روی سطح قطعات آنها را در محلول قلیایی حاوی L/g 20 کربنات سدیم یا پتاسیم و سپس در آب گرم غوطه ور می کنند. برای جلوگیری از خوردگی یا زنگ زدن ممکن است آبکشی در آب سرد نیز انجام بگیرد.
زنگ آهن، زنگ مس از طریق شستشو در اسیدهای معدنی رقیق حذف می شوند. برس کاری به راحت کنده شدن پوسته های سطح کمک می کند. در صورتی که بعد از اسیدشویی ابتدایی پوسته ها کاملاً پاک نشوند می توان عملیات را تکرار کرد.لکه های تیره نازک را می توان از طریق غوطه وری در محلول قوی سیانید پتاسیم (g/L 7)و چند قطره مایع آمونیاک پاک کرد. پوسته های اسیدی مس و روی در مخلوط 1 جزء اسید سولفوریک و 20 جزء آب بخوبی تمیز می شوند. برای پوسته های ضخیم تر باید از محلول اسیدی غلیظ تری استفاده کرد.زنگ آهن روی قطعات فولادی یا چدنی بخوبی در محلول 6 جزء اسید سولفوریک، 1 جزء اسید هیدرولیک و 160 جزء آب حذف می شود. مدت زمان غوطه وری min1 یا بیشتر است. برای پاک کردن لکه های اسیدی قلع یا روی از محلول قلیایی داغ استفاده می کنند.
فرآیند جیوه دهی: در این فرآیند حدود 30 گرم جیوه را داخل ظرف شیشه ای ریخته و به آن 30 گرم اسید نیتریک رقیق شده توسط سه برابر آب مقطر اضافه می کنند. برای این که جیوه کاملاً حل شود مخلوط را آرام آرام گرم کرده به آن اسید می افزایند. در نهایت 4 لیتر آب به محلول فوق اضافه کرده و خوب به هم می زنند. با غوطه ور کردن قطعات برنجی مسی یا نقره آلمانی در این محلول لایه ای نازک و براقی از جیوه سطح آنها را می پوشاند.
تمیزکاری الکترولیکی: فرآیند حذف کردن پوسته های سطحی در محلول با استفاده از جریان الکتریسیته است. در این فرآیند قطعات را از کاتد یا آند آویزه کرده و در وانی حاوی محلولی که هدایت الکتریکی خوبی دارد مثل اسید یا سیانید غوطه ور می کنند. انتخاب نوع محلول (از نظر اسیدی یا قلیایی بودن)به موادی که باید تمیز شوند بستگی دارد. برای تمیز کردن لکه های اضافی گریس یا زنگ محلول قلیایی مناسب است. در اثر عبور جریان برای مدت 10 تا 15 دقیقه از محلول تمام زایده های سطحی حذف می گردند.
تمیزکاری مکانیکی: تمیزکاری مکانیکی مکمل تمیزکاری شیمیایی و الکتروشیمیایی است. در این روش ابتدا به منظور پاک کردن چربیهای سطحی قطعات را توسط محلول پتاس شستشو داده و سپس در محلول اسیدی غوطه ور می کنند. بعد از مدت زمان مناسبی قطعات را خارج کرده و آبکشی می نمایند. در این حالت با استفاده از برس سیمی (به صورت دستی یا سنگ دستی)می توان مواد زاید سطحی را براحتی حذف کرد.
سطح قطعات کوچک ریخته گری و پرسکاری را می توان از طریق چرخاندن در داخل بشکه ای تمیز کرد. در این روش سطح قطعات در اثر غلتیدن روی همدیگر و سایش پاک می شود. از طریق ساچمه پاشی نیز می توان سطح قطعات را تمیز نمود. در روش دیگر قطعات را داخل بشکه حاوی ساچمه های فولادی که توسط الکتروموتوری حول محور قائم می چرخد می ریزند در این روش در اثر لغزش ساچمه روی قطعات، سطحی تمیز با درخشندگی بالا به دست می آید. این روش برای براق کردن سطح قطعات بعد از آبکاری نیز به کار می رود.
آبکاری مس:
آب مس به عنوان پوشش زیرین،در سیستم چند پوششی،عایق حرارتی برای انتقال حرارت،در الکتروفرمینگ و در بردهای مدار چاپی به طور گسترده ای مورد استفاده قرار می گیرد. اگر چه فلز مس در مقابل خوردگی نسبتاً مقاوم است،وقتی در مجاورت هوا قرار می گیرد به سرعت جلای خود را از دست می دهد و لک می شود. وقتی یک سطح زیبا و با دوام مورد نیاز باشد،آب مس به ندرت به تنهایی به کار می رود. آب مس براق در سیستم های چند پوششی،به عنوان پوشش زیرین محافظ مورد استفاده قرار می گیرد،یا وقتی تنها به عنوان پوشش تزئینی به کار می رود،توسط لایه ای از لاک شفاف در مقابل کدر و لک شدن،محافظت می شود،برای آبکاری مس می توان از الکترولیت های متعددی استفاده کرد که متداول ترین آنها عبارتند از:محلول های سیانید و پیروففات قلیایی،حمام های اسیدی سولفات و فلوئوبورات.
حمام های قلیایی آبکاری:
حمام های پروفسفات قلیایی به علت سرعت خوب آبکاری،اغلب برای ایجاد پوشش ضخیم به کار می روند،هر چند که باید به دقت کنترل شوند. با استفاده از حمام های سیانید قلیایی که کنترل آنها نسبتاً آسان است،می توان پوشش های نازکی با ضخامت یکنواخت به دست آورد. با توجه به قابلیت های بالای پوشش دادن این حمام ها بیشترین کاربرد را دارند. حمام های سیانید رقیق و سانید را شل برای ایجاد پوشش نازکی از مس به ضخامت m μ 3 تا (0.05-0.1mil)1.0 بیش از آبکاری مس و یا فلزات دیگر مورد استفاده قرار می گیرند. حمام های سیانید را شل غلیظ برای ایجاد پوشش هایی تا ضخامت حدود m μ 8 (0.3mil)، کاملاً مناسب هستند. با یک تغییر کوچک در تغییر الکترولیت را شل در آبکاری با الکترولیت ثابت، با همزن مکانیکی یا برای بازدهی بیشتر با هم زدن توسط هوا مورد استفاده قرار می گیرد. همچنین در مواردی که جریان معکوس متناوب و یا جریان منقطع استفاده می شود نیز این الکترولیت کاربرد دارد. حمام های آبکاری سیانید مس با غلظت مس کم و سیانید آزاد زیاد،سطح قطعات مختلف را طی عملیات آبکاری تمییز می کنند. اگر چه از این الکترولیت ها نباید به منظور تمییز کردن استفاده نمود،ولی به هر حال این حمام ها توانایی ایجاد پوشش نازکی از مس روی قطعاتی که تمیز کردنشان مشکل است را دارند. استفاده از سایر حمام ها منجر به پوشش ناقص و چسبندگی ضعیف می شود.
حمام های سانید سدیم و پتاسیم با راندمان بالا
با اضفه کردن مواد افزودنی خاص به حمام های غلیظ،می توان از آنها برای تولید پوشش هایی با براقی و قدرت هم سطح کنندگی متفاوت و ضخامت هایی از 8 تا m μ 5 20mils)تا 0.3)استفاده کرد. این الکترولیت ها به طور معمول،پوشش های ضخیم،صاف و براقی ایجاد می کنند. به دلیل قدرت بالای پوشش این الکترولیت ها،نقاط گود و تو رفته نیز دارای پوشش ضخیم و یکنواخت می گردند. برای ایجاد پوشش های صاف و بدون حفره عموماً از مواد افزودنی خاصی در این حمام ها استفاده می شود. قبل از آبکاری در حمام های باراندمان بالا، ابتدا قطعات باید با یک لایه نازک مس به ضخامت حدود m μ (0.05mil)10 از یک الکترولیت رقیق سیانید مس پوشش داده شوند.
مشخصات حمام های باراندمان بالا عبارتند از:
- دمای نسبتاً بالا
- غلظت زیاد مس
- سرعت عمل بالا
سرعت آبکاری در این حمام ها 3 تا 5 برابر حمام های سیانید رقیق و سیانید راشل می باشد. قطعاتی که در این الکترولیت ها آبکاری می شوند،باید کاملاً تمییز شوند. در غیر این صورت پوشش ایجاد شده از کیفیت پایینی برخوردار خواهد شد. همچنین برای زدودن آلودگی های آلی،حمام باید مرتب تصفیه شود.کمپلکس های تشکیل شده از ترکیب سیانید پتاسیم و سیانید مس دارای حلالیت بیشتری از کمپلکس های ایجاد شده از ترکسیب سیانید سدیم و سیانید مس می باشند. استفاده از حمام سیانید بهتر از حمام سدیم سیانید است زیرا احتمال سوختن پوشش در لبه کمتر می شود. بنابراین امکان استفاده از دانسیته جریان بالاتر را فراهم می کند،در نتیجه سرعت آبکاری بیشتر می شود. در الکترولیت های با راندمان بالا برای یکنواخت کردن پوشش روی قطعات پیچیده از جریان منقطع استفاده می شود. با استفاده از جریان معکوس به صورت تناوبی،پوشش یکنواخت تر خواهد شد.معکوس کردن تناوبی جریان در این الکترولیت ها موجب کاهش خلل و فرج پوشش نیز می شود. ترکیبات و شرایط کار حمام های آبکاری سیانید مس در جدول 1 داده شده است.
استفاده از مواد افزودنی اختصاصی،سبب افزایش راندمان آندی و کاندی،افزایش خرده گیری آند و در نهایت موجب عملکرد بهتر این الکرتولیتها می شود. این مواد سبب براق شدن پوشش و همچنین ریز شدن دانه ها می شوند. افزودنی های اختصاصی برای کنترل تاثیرات آلودگی های آلی و غیر آلی نیز مورد استفاده قرار می گیرند.
حمام های پیروفسفات مس برای آبکاری چند پوششی تزئینی،بردهای مدار چاپی و به عنوان عایق در عملیات حرارتی فولادها به کار می رود. حدود غلظت و شرایط کار در جدول 2 داده شده است.
حدود غلظت ها (g/l (oz/gal |
مس | (5-3)38-22 |
پیروفسفات | (33-20)250-150 |
آمونیاک | (3/0-10/0)3-1 |
نسبت وزنی پیروفسفات به مس | (2/1-9/0)5/8-0/7 |
شرایط کار |
دما | (FÚ 140-105)Ú 60-40 |
دانسیته جریان | 0/7-0/1 (A/ft2 70-10) |
راندمان کاند | %100-95 |
ولتاژ در تانک | V5-2 |
PH با دستگاه | (a)8/8-0/8 |
آندها | مس |
(a با اسید پروفسفریک و هیدرواکسید پتاسیم می توان ثابت نگه داشت |
خواص حمام پیروفسفات مس،حد واسطی بین حمام های اسیدی و سانیدی است،و بیشتر شبیه حمام سیانید با راندمان بالا سیانید با راندمان بالا می باشد. راندمان الکترود 100% است و قدرت پوشش دادن و سرعت آبکاری تا وقتی که حمام در PH تقریباً خنثی عمل می کند،خوب است. پوشش های به دست آمده حاوی دانه های ریز و نیمه براق هستند. هنگام استفاده از حمام پیروفسفات برای آبکاری فولاد،قطعات دای کاست از جنس روی،منیزیم،آلومینیم باید از یک پوشش اولیه بسیار نازک استفاده کرد. برای ایجاد این پوشش نازک،می توان از محلول سیانید رقیق مس یا پیروفسفات مس،نیکل یا محلول های دیگر استفاده کرد.
حمامهای آبکاری اسیدی:
از حمامهای اسیدی بطور گسترده در الکترورمینگ و تصفیه الکتریکی مس،تهیه پودر مس و آبکاری تزئینی استفاده می شود. این حمامها شامل مس دو ظرفیتی بوده، قابلیت داشتن ناخالصی های یونی بیشتری نسبت به حمام های قلیایی دارند،اما قدرت پوشش دادن ضعیف تری برخوردارند. خلل و فرج حاصل از حمام اسیدی کمتر است که در پر کردن تخلخل های قطعات دای کاست بسیار موثر می باشد. بیش از آن که فولاد یا آلیاژ روی دای کاست در حمام اسیدی مس آبکاری شود،باید در حمام رقیق سیانید مس یا نیکل پوشش داده شود.
پوشش نازکی از نیکل مانع رسوب کردن مس و پوسته شدن پوشش می شود.
خواص پوشش:
عوامل مختلف در مراحل آماده سازی سطح و آبکاری،اثرات مهمی بر روی کیفیت پوشش مس ایجاد شده دارد. بعضی از آنها ممکن است اثر منفی بر میزان چسبندگی مس روی قطعه کار داشته باشند. برخی دیگر بر روی میزان خلل و فرج،براقی،سختی،زبری،پوسته شدن،لحیم کاری و هم سطح کنندگی تاثیر می گذارند.
● براق بودن: پوششهای مس براق اغلب در اثر افزودن مواد براق کننده به الکترولیت ایجاد می گردند. اگر چه فرچه کاری پوشش نیز منجر به براقی آن می شود آبکاری در حمامهای سیاتید غلیظ،در صورتی که با قلع جریان و یا معکوس شدن متناوب جریان صورت گیرد،نیز منجر به بهتر شدن براقی پوشش مس می گردد. فرچه کاری و پولیش الکتریکی قطعه قبل از آبکاری منجر به ایجاد پوشش صاف و نیمه براق در یک الکترولیت فاقد براقی می شود. اگر از الکترولیت حاوی براقی استفاده شود میزان براقی پوشش افزایش می یابد. فرچه کاری پوشش برای براق نمودن آن هزینه زیادی در بر دارد. آبکاری در حمامهای سیاتید دارای زاندمان بالا با جریان منقطع و یا جریان متناوب معکوس براقی پوشش را بهبود می بخشد. تکنیکهای پیشرفته ریخته گری و پرداخت مکانیکی قبل از آبکاری می توانند کیفیت پوشش مس را بهبود بخشند.
● چسبندگی: برای بدست آوردن چسبندگی مناسب،نوع سطح و نحوه آماده سازی آن بر اثر آبکاری بسیار مهم است.بطور کلی کیفیت پوشش در قطعات ریختگی و سطوح متخلخل در مقایسه با سایر قطعات پائین تر است. نوع جنس قطعه نیز از عوامل تعیین کننده است. در قطعات دایکاست با پایه منیزیوم یا آلومینیم،لایه ی زینکاته ای که بین قطعه و پوشش مس قرار می گیرد،عامل کنترل کننده و بحرانی می باشد.
● فولادهای ضد زنگ: سرعت فرو بردن قطعات از جنس فولاد ضد زنگ که سطوح آن کاملاً فعال شده به حمام آبکاری تاثیر مهمی در چسبندگی پوشش خواهد داشت. بعضی براقی های آلی ممکن است روی چسبندگی پوششهای بعدی تاثیر منفی داشته باشند. چسبندگی پوششهای مس از الکترولیتهای اسیدی هنگامی می تواند مناسب باشد که قطعه قبلاً توسط حمام رقیق مس پوشش نازکی داده شده باشد.
● خلل و فرج: میزان تخلخل پوشش مس را می توان با انتخاب نوع حمام آبکاری مس،ترکیب الکترولیت و کنترل آن،جنس قطعه و شرایط سطحی که باید آبکاری شود. کنترل نمود. میزان تخلخل روی یک سطح تعیین کننده روش پرداخت برای حداقل رساندن آ» می باشد. یک سطح متخلخل از مساحت جانبی بزرگی برخوردار است و برای آنکه راندمان آبکاری بالا باشد باید از دانسیته جریان بالایی استفاده کرد.
● پوسته شدن: سطح بیشتر در مورد قطعات با پایه روی به خصوص وقتی که قطعه آبکاری شده در معرض حرارت قرار می گیرد رخ می دهد ممکن است قطعات از جنس منیزیومی و یا آلومینیومی نیز پوسته شوند که علت آن می تواند کیفیت نامطلوب قطعات ریخته شده یا آماده نمودن نامناسب سطح و یا هر دو باشد. میزان پوسته شدن پوشش نازک مس روی قطعات ریخته شده با پایه روی که بعداً در معرض حرارت قرار می گیرد را می توان با کم کردن PH حمام سیانید از 6/12-12 به حدود 10 کاهش داد. از آنجایی که در این PH کم،ممکن است گاز خطرناک سیانید هیدروژن آزاد شود مراقبتهای لازم باید انجام شود. به همین دلیل تهویه خوب حمام امری ضروری است. پوسته شدن پوشش مس روی منیزیم و آلومینیم به خصوص در هنگام لحیم کاری و یا وقتی که قطعه در معرض حرارت قرار نگیرد پوسته شدن نمایان نمی گردد. بهتر است قطعات آلومینیمی و منیزیمی را که آب مس داده شده اند به طور آزمایشی در معرض حرارت کنترل شده که باید بعد ها متحمل شود،قرار داد. اگر چسبندگی در سطح تماس ضعیف باشد این امر موجب پوسته شدن پوشش قبل از آبکاری دیگر می گردد.
● زبری: زبری در پوشش اغلب در اثر وجود ذرات خارجی بر حمام ایجاد می شود. وجود این ذرات ناشی از تمیز نمودن نادرست و یا مهاجرت ذرات فلز مس و یا اکسید مس یک ظرفیتی ایجاد شده در آند به طرف کاند می باشد. چنین زبری به خصوص در الکترولیت سیانید سدیم غلیظ ایجاد می گردد و می توان با استفاده از کیسه های دور آند از به وجود آمدن آن جلوگیری کرد.
● قابلیت لحیم کاری: پوشش زمانی خوب است که:
الف – سطح مس عاری از اکسید باشد.
ب- پوشش به اندازه ی کافی ضخیم باشد.
ج- چسبندگی آب مس داده شده بسیار خوب باشد.
لحیم کاری مستقیم قطعاتی که پوشش مس داده شده و سپس در دستگاهی آب بندی شده که مورد استفاده قرار می گیرند امری معمولی است. برای قطعات الکترونیکی از جنس آلومینیم و منیزیم که کاربدهای فضایی دارند لحیم کاری امری متداول است. این قطعات باید قبل از لحیم کاری زینکانه شده و سپس آب مس داده شود. برای قطعاتی که در معرض هوا قرار می گیرند یک پوشش نهایی از جنس کادمیم کروماته شده یا قلع بر روی لایه مس در ایجاد قابلیت لحیم کاری و همچنین مقاومت در برابر خوردگی بسیار موثر است.
● سختی «الکترولیتهای سیانید بدون حضور معرفهای افزودنی نسبت به حمامهای اسیدی پوشش سخت تری ایجاد می کنند. استفاده از معرفهای افزودنی در تمامی الکترولیها موجب افزایش سختی پوشش می گردد. به طور کلی سختی پوشش مربوط به دانه های ریز است اما می توان سختی را بدون ریز کردن دانه نیز با جهت دادن صحیح کریستالها افزایش داد. در حمامهای اسیدی تغییر غلظت سولفات مس و یا اسید سولفوریک تاثیر چندانی روی سختی پوشش ندارد.
● هم ترازی: تاثیر بسیار مهمی بر روی ظاهر پوشش و نیز ظاهر محصول نهایی (وقتی که پوششهای دیگری نیز بر روی مس نشانده می شود)دارد. اغلب فلزی که باید پوشش داده شود صافی مطلوب را ندارد. می توان بر روی سطوح قطعات فلزی به طریق مکانیکی و یا شیمیایی کارکرد تا زبری سطح پیش از آبکاری کاهش یابد.
بعضی الکترولیتهای مس قدرت هم سطح کنندگی خوبی دارند. بدین ترتیب در هزینه پرداخت کاری سطح قبل از آبکاری و یا سایر طرق صاف کردن سطح صرفه جویی می شود. وقتی که به الکترولیتهای غلیظ پتاسیم،برخی معرفهای افزودنی اضافه شود و در حین آبکاری جریان منقطع و یا متناوب معکوس استفاده گردد،هم سطحی بسیار خوبی حاصل می شود.
الکترولیتهای سیانید پتاسیم غلیظ،مخلوط سدیم و پتاسیم و سیانید راشل(نه به اندازه الکترولیت سیانید غلیظ ولی تا حد قابل قبولی)خواص هم سطح کنندگی خوبی را با جریان منقطع و یا جریان معکوس متناوب ایجاد می کنند.
● مس در سیستمهای چند پوششی: آب مس اغلب به عنوان پایه برای پوششهای بعدی در سیستمهای چند پوششی مورد استفاده قرار می گیرد.
● هزینه: هزینه آبکاری مس به نوع تاسیسات بستگی دارد. در صورتی که تجهیزات مدرن،اتوماتیک باشند براقی ها و معرفهای مرطوب کننده بیشترین هزینه را در بر دارد. چنانچه عملیات در مخزن ثابت انجام گیرد. هزینه کارگر مهمترین عامل است. افزایش دانسیته جریان سبب کاهش زمان لازم برای ایجاد پوشش با ضخامت معین می گردد و در نتیجه هزینه پایین می آید به کمک شکل 5 می توان هزینه مس رسوب کرده روی قطعه را که عملیات آبکاری عادی و متداول است تخمین زد. به عنوان مثال شکل 5 نشان می دهد که gr 20(oz4)مس لازم است برای آبکاری ناحیه ای به مساحت (VFt2)0.7m2 با پوششی به ضخامت 20 میکرون (0.8 mhl)است. هزینه پوشش مس با ضرب کردن وزن مس مورد نیاز در هزینه آندهای مسی بدست می آید. برای مساحتهایی بیشتر از (10Ft2)24m2 این مقدار را باید در فاکتور مناسبی ضرب نمود.
اصول آبکاری
به طور کلی ترسیب فلز با استفاده از یک الکترولیت را میتوان به صورت واکنش زیر نشان داد:
فلز
ترسیب فلز با روشهای زیر انجام میشود:
آبکاری الکتریکی
در این روش ترسیب گالوانیک یک فلز بر پایه واکنشهای الکتروشیمیایی صورت میگیرد. هنگام الکترولیز در سطح محدود الکترود/الکترولیت در نتیجه واکنشهای الکتروشیمیایی الکترونها یا دریافت میشوند (احیا)و یا واگذار میشوند (اکسیداسیون). برای اینکه واکنشها در جهت واحد مورد نظر ادمه یابند لازم است به طور مداوم از منبع جریان خارجی استفاده شود. واکنشهای مشخص در آند و کاتد همچنین در الکترولیت همیشه به صورت همزمان صورت میگیرند. محلول الکترولیت باید شامل یونهای فلز رسوبکننده باشد و چون یونهای فلزها دارای بار مثبت می باشند به علت جذب بارهای مخالف تمایل به حرکت در جهت الکترود یا قطبی که دارای الکترون اضافی میباشد (قطب منفی یا کاتد)را دارند. قطب مخالف که کمبود الکترون دارد قطب مثبت یا آند نامیده میشود. به طور کلی سیکل معمول پوششدهی را میتوان به صورت زیر در نظر گرفت:
- یک اتم در آند یک یا چند الکترون از دست میدهد و در محلول پوششدهی به صورت یون مثبت در میآید.
- یون مثبت به طرف کاتد یعنی محل تجمع الکترونها جذب شده و در جهت آن حرکت میکند.
- این یون الکترونهای از دست داده را در کاتد به دست آورده و پس از تبدیل به اتم به صورت جزیی از فلز رسوب میکند.
قوانین فارادی
قوانین فارادی که اساس آبکاری الکتریکی فلزها را تشکیل میدهند نسبت بین انرژی الکتریکی و مقدار عناصر جا به جا شده در الکترودها را نشان میدهند.
قانون اول: مقدار موادی که بر روی یک الکترود ترسیب میشود مستقیما″ با مقدار الکتریسیتهای که از الکترولیت عبور میکند متناسب است.
قانون دوم:مقدار مواد ترسیب شده با استفاده از الکترولیتهای مختلف توسط مقدار الکتریسیته یکسان به صورت جرمهایی با اکیوالان مساوی از آنهاست.
بر اساس این قوانین مشخص شده است که 96500 کولن الکتریسیته (یک کولن برابر است با جریان یک آمپر در یک ثانیه)لازم است تا یک اکیوالان گرم از یک عنصر را رسوب دهد یا حل کند.
آبکاری بدون استفاده از منبع جریان خارجی
هنگام ترسیب فلز بدون استفاده از منبع جریان خارجی الکترونهای لازم برای احیای یونهای فلزی توسط واکنشهای الکتروشیمیایی تامین میشوند. بر این اساس سه امکان وجود دارد:
ترسیب فلز به روش تبادل بار (تغییر مکان)یا فرایند غوطهوری: اساس کلی این روش بر اصول جدول پتانسیل فلزها پایهریزی شده است. فلزی که باید پوشیده شود باید پتانسیل آن بسیار ضعیفتر (فلز فعال)از پتانسیل فلز پوشنده (فلز نجیب)باشد. و فلزی که باید ترسیب شود باید در محلول به حالت یونی وجود داشته باشد. برای مثال به هنگام غوطهور نمودن یک میله آهنی در یک محلول سولفات مس فلز آهن فعال است و الکترون واگذار میکند و به شکل یون آهن وارد محلول میشود. دو الکترون روی میله آهن باقی میماند. یون مس دو الکترون را دریافت کرده احیا میشود و بین ترتیب مس روی میله آهن میچسبد. و هنگامی که فلز پایه که باید پوشیده شود (مثلا آهن)کاملا″ توسط فلز پوشنده (مثلا مس)پوشیده شود آهن دیگر نمیتواند وارد محلول شود و الکترون تشکیل نمیشود و در نتیجه عمل ترسیب خاتمه مییابد. موارد استعمال این روش در صنعت آبکاری عبارت است از: مساندود نمودن فولاد٬ نقرهکاری مس و برنج٬ جیوهکاری٬ حمام زنکات٬ روشهای مختلف کنترل و یا آزمایش٬ جمعآوری فلز از حمامهای فلزات قیمتی غیر قابل استفاده (طلا)با استفاده از پودر روی.
ترسیب فلز به روش اتصال: این روش عبارت است از ارتباط دادن فلز پایه با یک فلز اتصال. جسم اتصال نقش واگذارکننده الکترون را ایفا میکند. برای مثال هنگامی که یک میله آهنی (فلز پایه)همراه یک میله آلومینیومی٬ به عنوان جسم اتصال در داخل یک محلول سولفات مس فرو برده میشود٬ دو فلز آهن و آلومینیوم به جهت فعالتر بودن از مس٬ به صورت یون فلزی وارد محلول میشوند و روی آنها الکترون باقی میماند و چون فشار انحلال آلومینیوم از آهن بیشتر است از این رو اختلاف پتانسیلی بین دو فلز ایجاد شده و الکترونها در روی یک سیم رابط٬ از سوی آلومینیوم به طرف آهن جاری میشوند. بنابراین مشاهده میشود که مقدار زیادی از یونهای مس محلول روی آهن ترسیب میشوند. ضخامت قشر ایجاد شده نسبت به روش ساده تبادل بار بسیار ضخیمتر است. از روش اتصال برای پوششکاری فلزات پیچیده استفاده میشود.
روش احیا: ترسیب فلز با استفاده از محلولهای حاوی مواد احیا کننده٬ روش احیا نامیده میشود. یعنی دراین روش الکترونهای لازم برای احیای یونهای فلزات توسط یک احیا کننده فراهم میشود. پتانسیل احیا کنندهها باید از فلز پوشنده فعالتر باشند٬ اما بابد خاطر نشان ساخت که اختلاف پتانسیل به دلایل منحصرا″ کاربردی روکشها٬ نباید بسیار زیاد باشد. برای مثال هیپوفسفیت سدیم یک احیا کننده برای ترسیب نیکل است ولی برای ترسیب مس که نجیبتر است٬ مناسب نیست. مزیت استفاده از این روش در این است که میتوان لایههایی با ضخامت دلخواه ایجاد نمود. زیرا اگر مقدار ماده احیا کننده در الکترولیت ثابت نگه داشته شود میتوان واکنش ترسیب را کنترل نمود. به ویژه غیر هادیها را نیز بعد از فعال نمودن آنها٬ میتوان پوششکاری کرد.
آماده سازی قطعات برای آبکاری
برای بدست آوردن یک سطح فلزی مناسب نخستین عملی است که با دقت باید صورت گیرد٬ زیرا چسبندگی خوب زمانی به وجود میآید که فلز پایه٬ سطحی کاملا تمیز و مناسب داشته باشد. بدین علت تمام لایهها و یا قشرهای مزاحم دیگر از جمله کثافات٬ لکههای روغنی٬ لایههای اکسید٬ رسوبات کالامین که روی آهن در درجههای بالا ایجاد میشوند را از بین برد. عملیات آماده سازی عبارتند از:
سمبادهکاری و صیقلکاری: طی آن سطوح ناصاف را به سطوح صاف و یکنواخت تبدیل میکنند.
چربیزدایی: طی آن چربیهای روی سطح فلزات را میتوان توسط عمل انحلال٬ پراکندگی٬ امولسیون٬ صابونی کردن و یا به روش تبادل بار از بین برد.
پرداخت: انحلال شیمیایی قشرهای حاصل از خوردگی روی سطح فلزات را پرداخت کردن مینامند که اساسا″ به کمک اسیدهای رقیق و در بعضی موارد توسط بازها انجام میگیرد.
آبکشی٬ خنثیسازی٬ آبکشی اسیدی٬ خشک کردن: خنثیسازی برای از بین بردن مقدار کم اسید یا مواد قلیایی که در خلل و فرج قطعه باقی میمانندو همچنین آبکشی اسیدی برای جلوگیری از امکان تشکیل قشر اکسید نازک غیر قابل رؤیت که موجب عدم چسبندگی لایه الکترولیتی میشود.
موقعیت های استفاده از نانوتکنولوژی صنایع آبکاری
در سالهای اخیر نانوتکنولوژی که همان علم و تکنولوژی کنترل و بکارگیری ماده در مقیاس نانومتر است٬ تحقیقات فزاینده و موقعیتهای تجاری زیادی را در زمینههای مختلف ایجاد نموده است. یک جنبه خاص از نانوتکنولوژی به مواد دارای ساختار نانویی یعنی موادی با بلورهای بسیار ریز که اندازه آنها معمولا کمتر از 100 میکرومتر است میپردازد٬ که این مواد برای اولین بار حدود دو دهه قبل به عنوان فصل مشترکی معرفی شدند. این مواد نانوساختاری با سنتز الکتروشیمیایی تولید شدهاند که دارای خواصی از قبیل٬ استحکام٬ نرمی و سختی٬ مقاومت به سایش٬ ضریب اصطکاک٬ مقاومت ا